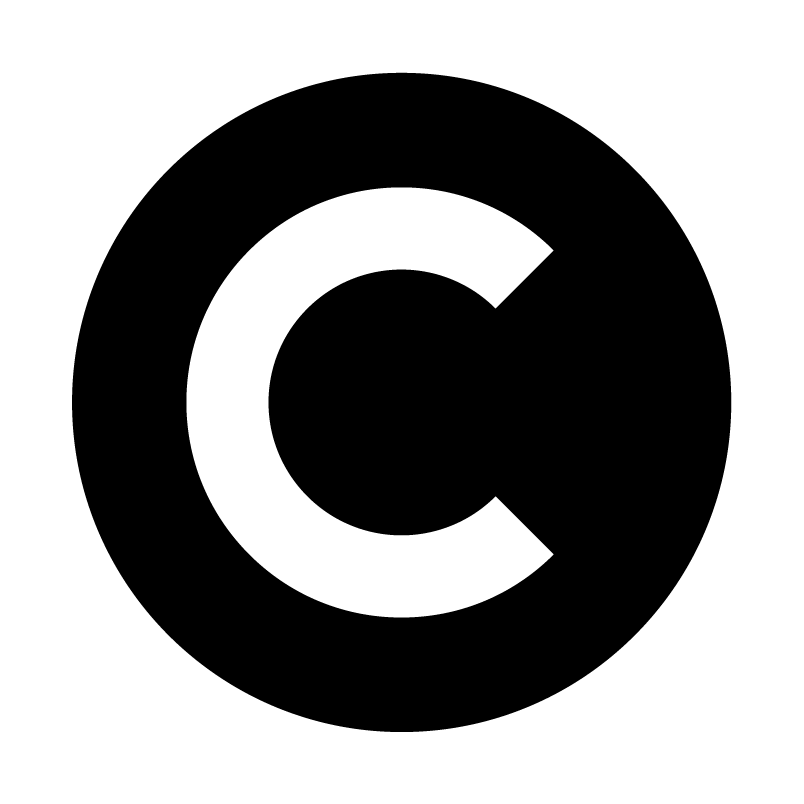
Cober Team
In today's digital age, while screens have become our primary source of information and entertainment, the enduring significance of print media can be underestimated. In fact, the print industry continues to evolve and adapt through the integration of cutting-edge technology.
Digital design and prepress
Technology's impact on the print industry begins long before the presses start rolling. The digital revolution has transformed the way designs are created and prepared for print. Design software have become indispensable tools for graphic designers. These applications enable designers to create stunning layouts, manipulate images, and precisely control typography, resulting in visually appealing printed materials.
Prepress technology has streamlined the process of preparing files for print. High-resolution scanning, color correction software, and digital proofing systems have made it easier to ensure that the final printed product matches the designer's vision. This has not only improved the quality of print materials but also reduced the time and cost associated with traditional prepress and proofing methods.
Printing technology advancements
Technology at Cober is one of the key ingredients to our growth and success. It is a fully stocked toolbox that allows us to easily connect with our customers and partners and connecting them to a highly integrated, manufacturing and shipping system capable of producing and delivering complex printed material in larger volumes and faster timelines than ever before.
— Erwin Driver, VP Technology at Cober Solutions
The heart of the print industry lies in the printing process itself. Technological advancements in printing methods have led to greater efficiency, flexibility, and quality. Here are some key technologies that have revolutionized the printing process:
Digital Printing: Digital printing has become increasingly popular due to its ability to produce high-quality, short-run prints with variable data. It eliminates the need for traditional printing plates and allows for on-demand printing, reducing waste and cost.
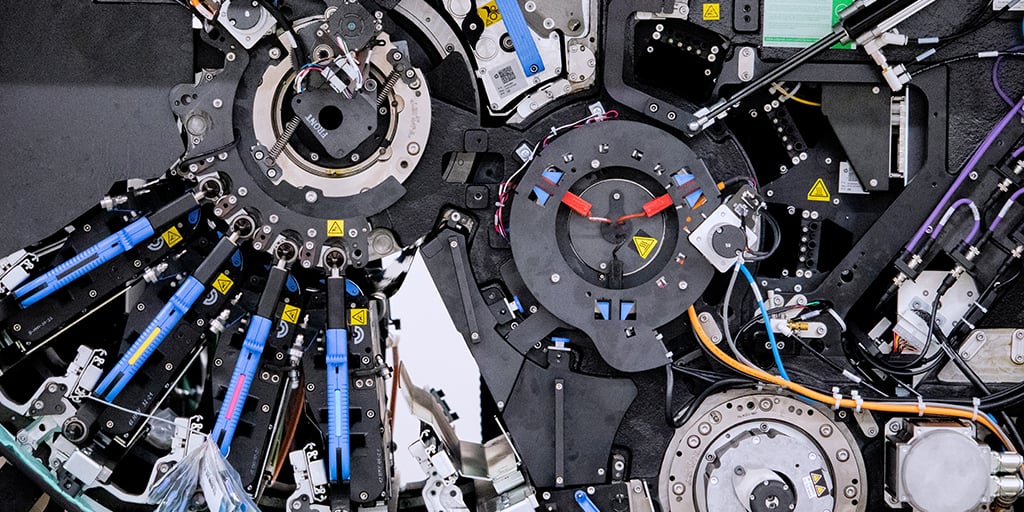
Offset Printing: Traditional offset printing has also benefited from technological improvements, including computer-to-plate (CTP) systems that replace film with digital data. This streamlines the plate-making process, reduces errors, enhances print quality, and reduces waste as well as the use of harmful developing chemicals.
Automation and workflow management
Modern print shops rely on sophisticated software and automation to manage workflow efficiently. Print management software helps streamline production by automating tasks such as job scheduling, inventory management, and quality control. This not only reduces human error but also optimizes resource allocation, leading to cost savings.
Furthermore, automation extends to the printing process itself. Automated printing and finishing equipment can handle large volumes of work with minimal human intervention, improving productivity and consistency.
Key advancements in digital prepress workflows include:
Computer-to-Plate (CTP) technology: CTP systems have replaced the older computer-to-film (CTF) methods. CTP technology directly transfers digital files to printing plates, reducing the risk of errors and improving image quality.
High-Resolution scanning: High-quality scanning technology enables prepress professionals to capture and digitize images and artwork accurately. This is particularly important when working with legacy print materials.
Digital proofing: Digital proofing systems allow for accurate color representation and on-screen proofing, reducing the need for physical proofs and the associated time and cost.
RIP (Raster Image Processor) technology: RIP software processes digital files into printer-ready data, ensuring that colors, fonts, and graphics are faithfully reproduced on the printed page.
Plate-to-Unit technology: This technology allows printing plates to be transferred fully automatically to the individual printing units and the used plates are removed. This allows for consistently high productivity with short print runs.
Sustainable practices
Technology has played a pivotal role in making the print industry more environmentally sustainable. Printing companies have adopted eco-friendly practices, including:
Recycling and waste reduction: Digital workflows have reduced the need for excessive paper proofs and waste, while eco-friendly inks and toners have become commonplace. Additionally with digital prepress, technology printers can maximise sheet usage, fitting multiple jobs onto one sheet and reducing cut off waste.
Energy efficiency: Advanced printing equipment consumes less energy and produces fewer emissions, contributing to a smaller carbon footprint.
Sustainable materials: Technology has made it easier to source and use sustainable paper and packaging materials, meeting the growing demand for eco-conscious printing.
Personalization and variable data printing
One of the most exciting developments in the print industry is the ability to personalize printed materials using variable data printing (VDP). VDP technology allows for the customization of printed content, such as names, addresses, and images, to create highly targeted marketing materials. This personalization enhances engagement and response rates, making print marketing more effective in the digital age.
Technology has played a transformative role in the print industry, reshaping everything from design and production to distribution and sustainability. While digital media continues to dominate our screens, print materials remain a powerful and enduring communication medium, thanks to the integration of cutting-edge technology. As technology continues to advance, we can expect even more innovation and evolution in the print industry, ensuring its relevance and vitality in the digital age.